Effect of Different Diluents on the Main Properties of the Epoxy-Based Composite
Received Date:April 22, 2020Accepted Date:May 17, 2020 Published Date:May 19, 2020
doi: 10.17303/jmsa.2020.4.104
Citation:Yasser Delavar barde (2020) Effect of Different Diluents on the Main Properties of the Epoxy-Based Composite.J Mater sci Appl 4: 1-9.
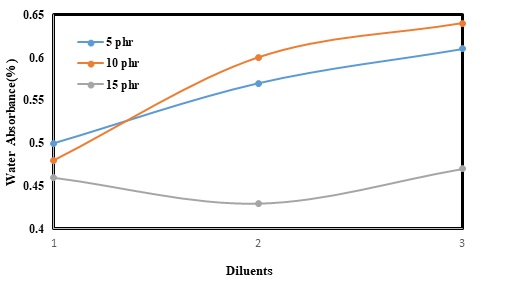
Abstract
The main purpose of this study was to investigate the effects of different types and concentrations (0, 5, 10, and 15 phr) of benzyl alcohol (BA), dibutyl phthalate (DBP), and 1,4- Butanediol diglycidyl ether (BDDE) as diluents on different properties of epoxy-based composites whose resin and hardener was RenLam LY 5138 and Aradur 5052; respectively. Some parameters including change in viscosity, gel time, contact angle, cross-linking percentage, and water absorption were accordingly monitored during the use of the diluents in the formulation. The results revealed that the viscosity and contact angle of the composites had sharply declined. However, viscosity had increased over time (about 85 min) for all three diluents (although the change in viscosity for BDDE was lower). Utilizing BA had also led to a significant decrease in gel time (about 66%). Nevertheless, DBP and BDDE had finally improved this parameter. Moreover, adding to BA and DBP concentrations had remarkably reduced cross-linking percentage (by 7%) while it had reached about 100% following the use of BDDE (10 phr). The lowest level of water absorption (at 30, 100) had further achieved once 15 phr of these three diluents had been employed.
Keywords: Epoxy resin; Hardener; Benzyl Alcohol; Diluent; Dibutyl Phthalate; 1,4-Butanediol Diglycidyl Ether
Introduction
The Vacuum Infusion Process (VIP) is known as a costeffective technique for producing large composite components for wind turbine blades, pressurized vessels, boats, etc. Within this process, one side of such objects is solid and the other side is a flexible vacuum bag, which is used to close the mold, and then resin is pushed into this mold by the force of the vacuum. Therefore, the success of the VIP depends on the low viscosity of the resin. This rheological behavior is needed to ensure complete infusion and fiber wetting [1,2,3]. The viscosity of resins is also commonly used in the VIP range between 500 and 1000 cps [4]. In the case of thermosetting resins, viscosity, hardening temperature, time, pressure, mixing ratio, and curing agent are mostly interdependent. For these resins, the performance of the final product is not a function of any one of these factors but is determined by the processing condition as a whole [5]. Thanks to their good mechanical, thermal, and chemical properties, epoxy resins can, therefore, have extensive uses in industry. One of the most popular groups of such substances is diglycidyl ether of bisphenol A (DGEBA)-based resins, with a viscosity of more than 10000 cps. Given the extensively high viscosity of such resins, it is common to utilize reactive diluents to modify their viscosity [6]. The desirable viscosity of the resin is thus considered as a fundamental requirement for its practical use in the industry [7]. In this study, diluents of epoxy resins were used to obtain a suitable resin for the VIP. Curing of epoxy resins also involves the conversion of liquid monomers into a three-dimensional (3D) network structure, affecting viscosity and processability time [8]. Besides, gelation is an important phase in curing of epoxy resins, referring to the state when the reaction has progressed enough to form a flexible 3D network. In epoxy systems, gelation also involves the release of heat and marks the end of the workability of the resin [9].
In this respect, an analysis of cured specimens has shown that adding up to 15% of diluents to the resin would not significantly change glass transition temperature, but using 20-30% of them would reduce glass transition temperature by 19-37°C [10]. Moreover, a study of mechanical properties has revealed that increased concentration of diluents does not have much effect on elastic modulus, but decreases tensile strength and augments percent elongation before fractures. These effects, attributed to matrix softening, can get stronger as the concentration of diluents is augmented [9]. Because of the proximity of epoxy groups to high-performance epoxy resins such as tetraglycidyl-4 and 4'-diaminodiphenylmethane, the etherification reaction is more common in these resins. As a result of frequent intermolecular etherification in these systems, their cross-linking density and higher glass transition temperatures have also grown. However, the level of etherification can be reduced using a stoichiometric ratio (r) closer to 1 (r = 1) [11].
Moreover, the glass transition temperature of a thermoset is directly related to the final transformation, the strength of chains, and the free volume trapped in a network. Therefore, it is difficult to induce movements in part of a polymer chain without expending very much energy for polymers with a high cross-linking density, high chain strength, and low trapped free volume [12-15].
Morteza Khalina, et al., investigated the influence of aliphatic reactive diluents on the main properties of two multifunctional and bifunctional epoxy resin. The results confirmed that the addition of the diluents causes decreasing the modulus and the ultimate strength of the resins. However, toughness and strain at break improved significantly [16].
In addition, the effect of two reactive (PEG) and none reactive (toluene) diluents on thermal and mechanical properties of DGEBA epoxy resin was studied via Amimesh Sinha and coworkers [17]. In fact, by using about 10wt% of the diluents, the thermal stability diminished remarkably. However, Mechanical properties such as hardness, fracture toughness, and tensile strength improved while 10wt% of PEG diluents were utilized. The examinations in this study were performed on three diluents i.e. BDDE, BA, and DBP. In the course of the study, the formulations were also found to be ill-suited for different phases and the VIP was eliminated until the final formulation was obtained
Materials and Method
This study was performed using epoxy resin with a hardener agent manufactured by Huntsman Co. (USA). Benzyl alcohol (BA), dibutyl phthalate (DBP), and 1,4-butanediol diglycidyl ether (BDDE) were accordingly used as diluents. The main characteristics of these ingredients are shown in Tables 1 and 2.
Equipment
A Brookfield viscometer model DV-III (Brookfield, United States), an Olympus microscope model: BX51 (Japan), a rotary vane vacuum pump (Poosh Co.: Iran), a Soxhlet extractor (Goldis Co.: Iran), and a mechanical mixer (Vari-Lab) (Jencons Co.: UK) were utilized as the main instruments in this study.
Characterization
Viscosity was measured using the Brookfield viscometer DV-III with the spindle #62 and rotation frequency of 10-rpm at constant temperature (25) based on ISO 165 [18]. Gel time was then measured according to [19]. Cross-linking percentage and levels of water absorption were correspondingly measured based on [20] and [21] respectively. The contact angle of the composites was finally calculated using the Olympus microscope and the AutoCAD Design 2013 software.
Methods
In this experiment, the special ratio of resin: hardener (100:43) was mixed via a mechanical mixer. Besides, different types and concentrations of the diluents were added to the mixture.
Results and Discussion
Effect of Diluents on Viscosity of Epoxy-Based Composites
The effect of diluents on the viscosity of the epoxy-based composites is depicted in Figure 1. The results confirmed that using BA had decreased viscosity in a linear manner. Increasing BA content from 0 to 9 phr had sharply reduced viscosity of the composites from 700 to 350 cP. Moreover, viscosity had not remarkably changed while BA content had improved from 9 to 12 phr. Finally, adding 15 phr of the diluent had resulted in a decline in viscosity to less than 200 cP.
In this experiment, a change in viscosity of the prepared composites was also monitored (Table 3) for a certain period (85 min.) at 25. Controlling change in viscosity of the blanket sample also showed that viscosity of the sample had significantly increased from 720 to 1849 cP within 85 min. In addition, the results confirmed that increasing the content of the diluents from 5 to 15 phr had led to a decrease in viscosity. Moreover, changes in the samples including BDDE in the formulation were the lowest. This diluent had an epoxy-based structure as an active diluent. As a result, the diluent could make a bond with other resins and hardeners in the formulation.
Gel Time
Gel time or the total time needed for complete curing of the epoxy resin is known as one of the most important parameters for each epoxy-based composite. Many different parameters may thus contribute to total gel time. As shown in Figure 2, the gel time of the blanket sample was about 370 min. Subsequently, gel time changed remarkably using different contents of the diluents. In other words, gel time declined from 300 to under 100 min as concentrations of BA increased from 5 to 15 phr. However, adding DBP and BDDE led to a sharp rise in gel time. Growing concentration of DBP resulted in improvements in gel time and it reached the maximum level of 450 min (for 15 phr). In addition, the same trend was achieved for BDDE. Changes in BDDE content from 5 to 15 phr enhanced gel time approximately from 420 to 450 min.
Contact Angle
The contact angle could directly influence adhesion and wettability of the composites. As a result, changes in contact angle might be one of the main parameters that must be taken into consideration. The effect of different types and concentrations of the diluents is illustrated in Table 4. It should be noted that diluents are usually used in order to decrease the viscosity of epoxy resins. So, it seems that the utilization of diluents is very vital. However, the results confirmed that the diluents had negative effects on the contact angle of the composites (Table 4 and Figure 3). Moreover, the results demonstrated that the contact angle of the sample without any diluents (i.e. blanket) was about 53.45. By adding 5 phr of BA, the contact angle had also significantly decreased (from 53.45 to 48.2). Subsequently, DBP and BDDE had led to a decline in contact angle up to 45.2 and 44.7; respectively. Increasing the content of the diluents from 5 to 10 phr and 15 phr had additionally resulted in a descending trend in contact angle. Finally, the minimum contact angle had been achieved (about 36.87) once the 15 phr of BA had been utilized.
Cross-Linking Percentage and Level of Water Absorption
When the hardener was added into the mixture of the resin, cross-links were made. Most of the properties of the epoxybased composites also depended on the cross-linking percentage. Besides, this property of the mixture directly depended on resin: hardener ratio and some other ingredients. Accordingly, investigating the effect of the diluents on cross-linking percentage confirmed that (Figure 4) adding BA and DBP could have negative impacts on cross-linking percentage of the composites. Increasing BA and DBP contents from 5 to 15 phr could change the cross-linking percentage from 96 to 90% and 95 to 91%; respectively. However, the results established that BDDE had improved cross-linking percentage. In other words, using 5 phr of this diluent had resulted in an increase in cross-linking percentage from 98 (blanket sample) to 99%. Moreover, the highest level of cross-linking (about 100%) was achieved when 10 phr of BDDE was utilized.
Epoxy-based composites are usually applied in outdoor environments. As a result, the resistance of such composites against humidity, heat, and light can be the most important parameter. Resistance against humidity or water absorption is thus a vital problem facing these composites. It can be more problematic when the composites used for a long time cause inflation and finally degradation. Different parameters can also affect the water absorption of epoxy resins. In this experiment, the effect of diluents was studied at two different temperatures i.e. 30 and 100 (Figure 5 and Figure 6). The results also confirmed that increasing BA concentration from 5 to 15 phr could result in a slight decrease in levels of water absorption from 0.5 to 0.46% at 30 Furthermore, water absorption could be about 0.56% as 5 phr of DBP was added. However, increasing the concentration of the diluents to 10 phr had augmented levels of water absorption and reached 0.6%. Improving DBP content from 10 to 15 phr, water absorption had also sharply decreased and reached the lowest level of 0.42 %. The same trend was additionally observed when DBP was replaced with BDDE. The lowest level of water absorption was obtained (0.46%), while 15 phr of BDDE was employed.
Water absorption can be also directly correlated with temperature. So, it is clear that increasing temperature from 30 to 100 can lead to a rising trend in levels of water absorption of the epoxy-basedd composites. Water absorption was also equal to 0.7% as 5 phr of BA was added. Subsequently, replacing BA with DBP and BDDE could increase water absorption to 0.75% and 0.77%; respectively. Adding to the concentration of the diluents from 5 to 10 phr had further resulted in a slight increase in water absorption. The lowest and the highest levels of water absorption (at 10 phr concentration) belonged to BA (0.78%) and BDDE (0.9%); respectively. However, utilizing 15 phr of the diluents could significantly decrease water absorption and the lower peak of water absorption was achieved (about 0.6 %) when DBP was used.
Conclusion
This study reflected on the effects of different types of diluents on the main properties of epoxy-based composites with ingredients including resin (RenLam LY 5138) and hardener (Aradur 5052). In addition, three different diluents such as BA, DBP, and BDDE in different concentrations (0, 5, 10, and 15 phr) were used in the formulation. Accordingly, the results confirmed that using different contents of diluents could have negative effects on the viscosity and contact angle of the prepared composites. Moreover, time passing revealed that viscosity had not remained stable. The viscosity increased over time for all the formulations after about 85 min. In other words, change in viscosity for the formulation including BA was more than that for DBP and the minimum level belonged to BDDE samples. Measuring the gel time of the prepared composites also made it clear that increasing BA content from 5 to 15 phr had resulted in a decrease in gel time from 300 to 100 min. However, the use of the two other diluents increased gel time compared with the blanket. Adding to the concentration of BA and DBP remarkably decreased the cross-linking percentage (about 7%) while it reached about 100% as BDDE (10 phr) was employed. Ultimately, the lowest level of water absorption (at 30, 100) was achieved once 15 phr of these three diluents were utilized.
Acknowledgment
This study is financially supported by the Ferdowsi University of Mashhad (No. 3/39581) and the help of Sun-Air Research Institute (university campus, Mashhad, Iran) in developing this project.
Contribution Statement
All authors contributed to the study conception and design. Material preparation, data collection, and analysis were performed by Yasser Delavar barde. The first draft of the manuscript was written by Moein Behzadpour and all authors commented on previous versions of the manuscript. All authors read and approved the final manuscript.
- Yang j, Xiao j, Zeng j, Peng C, Feng X, Hou B (2012) An Empirical Model for Resin Viscosity during Cure in Vacuum Infusion Molding Process. Appl Compos Mater 19: 573–582
- Correia NC, Robitaille F, Long AC, Rudd CD, Simacek P, Advani SG (2005) Analysis of the vacuum infusion moulding process: I Analytical formulation. Composites: Part A 36: 1645–1656.
- Modi D, Correia N, Johnson M, Long A, Rudd C, Robitaille F (2007) Active control of the vacuum infusion process. Composites: Part A 38: 1271–1287.
- Brouwer WD, van Herpt ECFC, Labordus M (2003) Vacuum injection moulding for large structural applications. Composites: Part A 34: 551–558.
- Cheng KC, Chiu WY, Hsieh KH (1994) Chemo rheology of epoxy resin Part I Epoxy resin cured with tertiary amine. J Mater Sci 29: 721–727
- Liu MH, Hou HY, Peng HJ, Li M (2015) the influence of the active diluents cyclohexene oxide on the curing processing. Journal of thermal analysis and calorimetry 122: 509–515.
- Tucker SJ, Fu B, Kar S, Heinz S, Wiggins JS (2010) Ambient cure POSS–epoxy matrices for marine composites. Composites: Part A 41: 1441–1446.
- Garschke C, Parlevliet PP, Weimer C, Fox BL (2013) Cure kinetics and viscosity modelling of a high-performance epoxy resin film. Polymer Testing 32: 150–157.
- Solodilov VI, Gorbatkina Y, Kuperman M (2003) The effect of an active diluent on the properties of epoxy resin and unidirectional carbon-fiber-reinforced plastics Mechanics of Composite. Materials 39: 493–502.
- Nunez-Regueira M, Fragra-Rivas I (2006) Effect of a reactive diluent on the curing and dynamomechanical properties of an epoxy-diamine system. Journal of Thermal Analysis and Calorimetry 86: 463–468.
- Bonnaud L, Pascault JP, Sautereau H (2000) Kinetic of a thermoplastic-modifed epoxy- aromatic diamine formulation: modeling and influence of a trifunctional epoxy prepolymer European Polymer Journal 36: 1313–1321.
- Smith C (1984) the glass transition temperature and its measurement in epoxy glass laminates. Circuit World. 122: 62–64.
- Nielsen LE (1969) Cross-linking-effect on physical properties of polymers. Journal of Applied Polymer Science. 69–103.
- Jain P (2003) Effect of structure on thermal behavior of epoxy resins. European Polymer Journal 39: 181–187.
- Pascault JPP, Williams RJJ (2010) General Concepts about epoxy polymers in Epoxy polymers. Wiley‐VCH Verlag GmbH & Co. KGaA. Germany
- Khalina M, Beheshty MH., Salimi A (2018) The effect of reactive diluent on mechanical properties and microstructure of epoxy resins, Polymer Bulletin volume 76: 3905–3927.
- Sinha A, Islam Khan N, Das S, Zhang J, Halder S (2019) Effect of reactive and non- reactive diluents on thermal and mechanical properties of epoxy resin, High Performance Polymers 10: 1159- 1168.
- ISO 1652 (2011) Rubber latex — Determination of apparent viscosity by the Brookfield test method.
- ASTM D2471-99 (2008) Standard Test Method for Gel Time and Peak Exothermic Temperature of Reacting Thermosetting Resins.
- Wenshu G, Chang L, Jianwu L, Qingxin Z, Nongyue W, Beckry AM, Xiongwei Q (2019)Effect of the Crosslinking Agent Content on the Emulsion Polymerization Process and Adhesive Properties of Poly(N-Butyl Acrylate-Co-Methacrylic Acid). Journal of adhesion science and technology 33: 2031-2046
- ASTM D570 - 98 (2018) Standard Test Method for Water Absorption of Plastics.
Figures at a glance