The Influence of Aging Treatment on the Microstructural and Mechanical Behavior by Ultra-Micro Hardness Tester in Ni-Rich NiTi Alloy
Received Date: July 27, 2020 Accepted Date: August 18, 2020Published Date: August 20, 2020
doi: 10.17303/jmsa.2020.4.105
Citation:Rodolfo Teixeira (2020) The Influence of Aging Treatment on the Microstructural and Mechanical Behavior by UltraMicro Hardness Tester in Ni-Rich NiTi Alloy. J Mater sci Appl 4: 1-6.
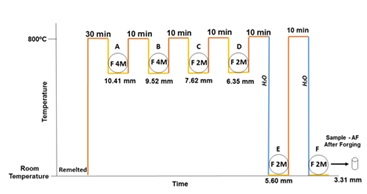
Abstract
The present study aims to assess the superelasticity behavior in Ni-rich NiTi alloy wire produced by the rotary forging process. The thermomechanical process involved four steps of hot working at 800ºC, two steps of cold working with solution heat treatment at 800ºC between them, and subsequently, a solution heat treatment (950ºC during 2 hours) followed by aging treatment at 350, 400 and 450ºC during 30 minutes. X-ray diffraction (XRD) and instrumented ultra-micro hardness testers evaluated the present phase at each aged sample and were compared with their mechanical behavior. The results put in evidence the work-hardening effect on a forged condition associated with the final step of cold rotary forging. The solution treatment promotes stress relaxation and precipitate dissolution. The sample heat-treated shows the presence of the precipitated (Ni4 Ti3) and R phase. The presence of these precipitates is beneficial because precipitation-hardening increases the yield strength of austenite, which in turn contributes to better functional stability.
Introduction
Many factors can interfere on some materials final characteristics (phase transformations, shape memory effect or its superelasticity at a given working condition), namely: thermal and thermo-mechanical treatments; the Ni and Ti content; alloying elements addition; the presence of impurities such as C, N and/or O; and microstructure. Therefore, follow up the chemical composition, and the thermo-mechanical process variables are mandatory [1–6]. NiTi processing needs to have both hot and cold forming, since surface finishing, microstructure refinement and improvement of the mechanical properties are achieved during the cold processing [5,7–9]. Thus, when it is desired to obtain distinct functional properties such as superelasticity and shape memory effect, these alloys require a proper thermal treatment after the cold forming step. As the heat treatment temperature decreases, the presence of plastic deformation in the material and austenitic phase resistance increases. However, a decrease in the ductility is also observed; therefore, it improves the superelasticity effect, reduces the residual strain while increasing the capacity to absorb energy resulting in the prevention of permanent deformation [10–12]. The austenite and/or R phase (by precipitates) presence at room temperature in Ni-rich NiTi alloys can be achieved by thermal aging treatments [8,13–15]. Gall et al. (2001)[16] observed the mechanical properties through analyzing the areas resulted by the instrumented nanoindentation test based on prior microstructural conditions, between loading and unloading curves. This test allows us to determine dissipated energy, material hardness, the plastic and elastic working behavior (dissipated and recovery energies), and recoverable energy mechanisms that occur internally within the microstructure.
Since the extracted data in this graphic representation allows us to infer the mechanical behavior of the resulting microstructural condition associated with heat treatment applied to the sample.
When stress is applied to the austenite field, the induced-stress martensite is formed, but after unloading, the deformed material reverts to austenite [18–21].
Therefore, this study aimed to evaluate the superelastic development, the influence of aging treatment, and correlate the resulting phase at room temperate in Ni-rich NiTi alloy thin bars produced by rotary forging.
Material and Methods
Ni-rich NiTi alloy, produced by the melting process in a vacuum induction furnace (VIM) at “Instituto Tecnológico da Aeronaútica” (ITA) – Brazil, with approximately 50.8 at. % Ni was used in this study. The ingot slice was cut by electroerosion to get samples with 90 g each and then recast in the arc melting furnace to obtain cylindrical samples for the thermomechanical processing by rotary forging, which started with a sequence hot forming and finished by cold-work sequences interspersed with steps of heat treatment, as shown in Figure 1.
The material was solubilized at 950°C for 120 minutes, and/or with further aging treatment at 350ºC, 400ºC, 450ºC for 30 minutes, followed by quenching into the water at room temperature.
Structural characterization of the specimens was performed using the XRD test (Shimadzu (XRD-6000)) diffractometer CoKα. The XRD test was performed at 20 ºC, controlled temperature. Mechanical properties were evaluated by Vickers indenter at 20°C, using an instrumented ultra-micro hardness tester (Shimadzu, DUH-211S) applying maximum force (F) of 25 gf. Results are the mean value of five measurements obtained from loading curves.
Results and Discussions
From XRD results (Figure 2) is possible to verify that both samples - After Forging sample (AF) and Solubilized sample (SOL) - are austenitic at 20 ºC (room temperature - controlled temperature). Although differences between their behavior could be observed, and are highlighted below:
- AF sample shows evidence of (110)B2 peak in 49.85 2θ, and the SOL sample shows (110)B2 peak in 49.6 2θ; The (110)B2peak at AF sample has higher intensity and a thin shape while the SOL sample has an inverse characteristic. Due to heating, it was evident that the austenite peak (110)B2 shifted to smaller 2θ angles in the SOL sample, corresponding to larger d-spacing. Besides, the intensity decreasing may be explained due to grain growth during solution heat treatment as supposed by larger d-spacing values. Therefore, revealing that this homogenization was efficient for the following aging steps adopted for this work. - Aged Sample at 350 ºC_30min, the presence of a mixture of B2 and R-phase was identified. Due to precipitation phenomena (Ni4 Ti3 ), the R-phase also can be observed. The aged samples at 400 and 450 ºC_30 min show the 2θ position of (110)B2 peak close to the SOL sample (110)B2 2θ position. Besides, the broadening of the (110)B2 peak may be associated with the presence of precipitates. These precipitates are distributed in the B2 matrix, affecting the mechanical characteristics of the alloy. The technique applied did not allow us to identify smaller precipitates.
Ni-rich Ni-Ti alloys can exhibit superelastic properties resulting from B2–B19’stress-induced transformation. For heat treatments at high temperatures, there is enough thermal energy to allow rapid diffusion of Ni and Ti atoms in the matrix. On the other hand, at a lower temperature nucleation rate is higher, but the diffusion coefficients are low. Both processes are equilibrated at intermediate temperatures (350 – 450 °C) to achieve maximum precipitation rates.[22]The size of the Ni4 Ti3 precipitates increases with increasing aging temperature and aging time [23,24].
Figure 3 demonstrates five measurements of ultra-micro hardness of the before (AF sample) and after solution treatment at 950 ºC for 2 hours (SOL sample) and different aged samples (350, 400, and 450 ºC for 30 minutes). The mechanical behavior (Figure 3) was analyzed by graphic interpretation, considering the behavior of curves. Analysis of nanoindentation curves conjugated to the analysis of XRD patterns (Figures2 and 3), it is possible to support its behavior. When comparing AF samples with SOL sample results (Figure 4(a, b)), it is possible to observe that both samples have similar behavior, may be associated with B2 at room temperature, even AF showed a displacement in B2 peak. The aged samples are subjected to Ni4 Ti3 precipitation that introduces stress fields, thus giving changes in transformations condition, and its respective phase presents at each heat treatment performed (Figures 2 and 3). As described below.
- For 350 ºC their behavior is analyzed (Figure 3(c)), which has plateau region, that suggests to occurs two effects isolated or simultaneously: i) reorientation of variants of the R-phase (Figure 2) and/or ii) martensitic transformation by stress-induced (B2 → R).
- For 400 and 450 ºC, no significant difference was identified. These results were not expected. All these aging temperatures showed B2 at room temperature (Figure 3). However, the reason for the absence of the plateau region could be interpreted as being a result of high maximum force and together with the absence of R-phase, which the tension associated with the reorientation of the R-phase variants is lower than a stress-induced transformation from B2.
Some properties from ultra-micro hardness tester of the AF sample, SOL sample, and different aged samples (350, 400, 450ºC for 30 minutes) are shown in Table 1.
The permanent indentation depth after removal of the test force (hp), reveals lower mean values to AF and SOL samples. Among the aged samples, 350 °C showed higher mean values.
The propriety indentation hardness, Hit, is a measure of the resistance to permanent deformation or damage. In qualitative terms, it can be related to the yield strength for advanced deformation [25]. The formula to obtain (Hit) is Hit = Fmax/Ap , where Fmax is maximum force, and A p is projected (cross-clauseal) area of contact between the indenter and the test piece determined. For triangular indenter (115°), Ap = 23.96 x hc². Higher mean values are checked for SOL and AF sample. It can be associated with the presence of the austenitic phase. The same behavior was checked to aged samples, higher mean values to the aged samples at 400, 450, and 350 °C. The 350 ºC sample shows lower mean values, and it could be due to the tension associated with the reorientation of variants of the R-phase (which is presumably present in this aging temperature, is placed in levels lower than B19 ’and much lower than the level of stress-induced transformation at from austenitic phase (B2)). These results corroborate with those observed to hp.
Conclusions
1 -The aging heat treatment performed at 350, 400, and 450 ºC indicated the formation of Ni4 Ti3 in the early stages of precipitation by R-phase identified in XRD measurement.
2 - Ageing conditions associated with lower heterogeneity precipitates distribution profile was more suitable to induced phase transformation by deformation than the promoted previous deformation by dislocations slip. Thus, the minimum (350°C) and maximum (450°C) aging temperature, adopted in this work, promoted an increase of the critical shear stress required for dislocation slip, stabilizing austenite at room temperature due to the Ni3 Ti4 precipitate formation early or later stages with homogeneous distribution trends on the B2 matrix.
3 – 350 ºC aged sample showed a mixture of the presence of austenite and R-phase at room temperature.
4 - The results indicated that, among the aging, conditions studied, the 350°C / 30min sample shows the best conditions for superelasticity associated with low critical stress for the stress-induced martensitic transformation.
4 - The instrumented ultra-micro hardness test has demonstrated to be a promising technique to evaluate superelastic behavior. It was identified in the plateau region. However, it may have limitations. It is plausible that the selected maximum force might have influenced the results obtained. These limitations underline evidence of the difficulty of collecting data from hardness.
Acknowledgments
Teixeira, R.S. acknowledges the funding of Capes. The authors thank FAPERJ for the financial support (APQ-1 2009/02 E-26/110.414/2010, APQ-1 2011-2 E-26/110.269.2012, E-26/111.435/2012) and to CAPES for a Ph.D. scholarship (S.B.R. and S.B.D. in Brazil, and P.R.F by CSF BEX 11943-13-0 in Portugal). PFR acknowledges the funding of CEMMPRE by Project PTDC/CTM-CTM/29101/2017 – POCI-01-0145-FEDER-029101 funded by FEDER funds through COMPETE 2020 - Programa Operacional Competitividade e Internacionalização (POCI) and by national funds (PIDDAC) through FCT/MCTES. This research is sponsored by FEDER funds through the program COMPETE – Programa Operacional Factores de Competitividade – and by national funds through FCT – Fundação para a Ciência e a Tecnologia –, under the project UIDB/00285/2020. The authors thank Professor Jorge Otubo for donating the starting materials that were produced in the Instituto Tecnológico da Aeronáutica (São José dos Campos, SP – Brazil). The authors thank Professors Ladário da Silva and José Augusto Oliveira Huguenin which allowed the use of the Laboratório Multiusuário de Caracterização de Materiais do Instituto de CiênciasExatas da Universidade Federal Fluminense (ICEx/UFF), in Volta Redonda/RJ - Brazil, for the use of the instrumented ultra-micro hardness equipment for analysis of the samples.
- Y Suzuki (1998) Fabrication of shape memory alloys. In: Otsuka K and CMW, editor. Shape Mem. Mater. 1st ed., New York: Cambridge University Press 133–148.
- Otsuka K, Ren X (2005) Physical metallurgy of Ti-Ni-based shape memory alloys. Prog Mater Sci 50: 511–678.
- Kotha RS, Alla RK, Shammas M, Ravi RK (2014) An Overview of Orthodontic Wires. Trends Biomater Artif Organs 28: 32–36.
- Otubo J, Rigo OD, Coelho AA, Neto CM, Mei PR (2008) The influence of carbon and oxygen content on the martensitic transformation températures and enthalpies of NiTi shape memory alloy. Mater Sci Eng A 481–482: 639–642.
- Zhou D, Gao Y, Lai M, Li H, Yuan B, Zhu M, et al. (2015) A review of shape memory alloy research, applications, and opportunities. Mater Sci Eng A 56: 1078–1113.
- Freitas Rodrigues P (2018) Structural Evolution of Ni-Ti Alloy Wires Produced by Hot and Cold Rotary Forging Dissertação para obtenção do Grau de Doutor em Ciência e Engenharia de Materiais. Universidade Nova de Lisboa
- Sun B, Lin J, Fu MW (2018) Dependence of processing window and microstructural evolution on the initial material state indirect electric resistance heat treatment of NiTi alloy. Mater Des 139: 549–564.
- Khalil-Allafi J, Eggeler G, Dlouhy A, Schmahl WW, Somsen C (2004) On the influence of heterogeneous precipitation on martensitic transformations in a Ni-rich NiTi shape memory alloy. Mater Sci Eng A 378: 148–151.
- Świec P, Zubko M, Lekston Z, Stróż D (2016) Structure and Properties of NiTi Shape Memory Alloy after Cold Rolling in Martensitic State. Acta Phys Pol A 130: 1081–1084.
- Nemat-Nasser S, Guo WG (2005) Superelastic and cyclic response of NiTi SMA at various strain rates and temperatures. Mech Mater 38: 463–474.
- Yeung KWK, Cheung KMC, Lu WW, Chung CY (2004) Optimization of thermal treatment parameters to alter austenitic phase transition temperature of NiTi alloy for a medical implant. Mater Sci Eng A 383: 213–218.
- Heller L, Seiner H, Šittner P, Sedlák P, Tyc O, Kadeřávek L (2018) On the plastic deformation accompanying cyclic martensitic transformation in thermomechanically loaded NiTi. Int J Plast 111: 53–71.
- Allafi JK, Ren X, Eggeler G (2002) The mechanism of multistage martensitic transformations in aged Ni-rich NiTi shape memory alloys. Acta Mater 50: 793–803.
- Schmahl WW, Khalil-Allafi J, Hasse B, Wagner M, (2004) Investigation of the phase evolution in a super-elastic NiTi shape memory alloy (50.7 at.%Ni) under extensional load with synchrotron radiation. Mater Sci Eng A 378: 81–85.
- Fan QC, Zhang YH, Wang YY, Sun MY, Meng YT, Huang SK, et al. (2017) Influences of transformation behavior and precipitates on the deformation behavior of Ni-rich NiTi alloys. Mater Sci Eng A.
- Gall K, Juntunen K, Maier HJ, Sehitoglu H, Chumlyakov YI (2001) Instrumented micro-indentation of NiTi shape-memory alloys. Acta Mater 49: 3205–3217.
- Morgan N, Wick A, Dicello J, Graham R (2008) Carbon and Oxygen Levels in Nitinol Alloys and the Implications for Medical Device Manufacture and Durability. Int. Conf. Shape Mem. Superelastic Technol., vol. 683, California: ASM International 821–828.
- Saghaian SM, Karaca HE, Tobe H, Pons J, Santamarta R, Chumlyakov YI, et al. (2016) Effects of Ni content on the shape memory properties and microstructure of Ni-rich NiTi-20Hf alloys. Smart Mater Struct 25: 095029.
- Gall K, Sehitoglu H, Chumlyakov YI, Kireeva IV, Maier HJ (1999) The Influence of Aging on Critical Transformation Stress Levels and Martensite Start Temperatures in NiTi: Part II—Discussion of Experimental Results. J Eng Mater Technol 121: 28– 37.
- Teixeira RS, Paula AS, Santos FS, Rodrigues PF, Braz Fernandes FM (2018) Critical Analyses on the Instrumented Ultra microhardness Results on Aging NiTi Alloy in Distinct Phase Fields 109–114.
- Rodrigues PF, Fernandes FMB, Texeira EN, Baptista S, Paula AS, Oliveira JP (2017) Influence of aging treatment on the thermophysical characteristics and mechanical properties of forging wire Ni-rich NiTi alloy for superelastic applications. Ciência Tecnol Dos Mater 29: e23–26.
- Pelton AR, Dicello J, Miyazaki S (2000) Optimisation of processing and properties of medical-grade Nitinol wire. Minim Invasive Ther Allied Technol 9: 107–118.
- Bataillard L, Bidaux JE, Gotthard R (1998) Interaction between microstructure and multiple-step transformation in binary NiTi alloys using in-situ transmission electron microscopy observations. Philos Mag A Phys Condens Matter, Struct Defects Mech Prop 78: 327–344.
- Wagner MFX, Dey SR, Gugel H, Frenzel J, Somsen C, Eggeler G (2010) Effect of low-temperature precipitation on the transformation characteristics of Ni-rich NiTi shape memory alloys during thermal cycling. Intermetallics 18: 1172–1179.
- (2009) Dynamic Ultra-micro Hardness Tester Instruction Manual.
Figures at a glance